Web Width Measurement - an Important Quality Parameter
Web width measurement is one of those applications that is usually an afterthought until reality bites. Converters might be faced with improving their process by reducing web edge trim or eliminating downtime due to web widths out of specification. Most importantly, they want their customers to be happy by avoiding delivering products that do not comply with customer web width requirements.
The industrial world knows that having a customer that trusts your product is one of the greatest assets. If your width monitoring process allows you to avoid delivering out of specification rolls, you will definitely have a satisfied returning customer. So, how can we help you in achieving satisfied customers?
Different Widths in the Same Converting Line - How converters currently deal with it.
When handling different web widths in the same converting line, the issue is having sensors that provide enough coverage. Typically you have two sensors and then you adjust their position to allow the sensors to see both edges of the web. This repositioning of sensors can be manual or electromechanical.
Manual Repositioning of Sensors
In manual repositioning an operator has to physically access the sensors and move them to the new position, calibrating the sensors to adjust for the change, and then estimate the actual distance between the sensors to provide a reference for the width measurement. In this system, there are issues of accuracy of the measurement, time lost in repositioning the sensors, and wear and tear of the equipment.
Electromechanical Repositioning of Sensors
With electromechanical repositioning an actuator moves the sensors to their positions. It still requires spending time to calibrate the sensors, move the sensors to the position required and verifying that it is the proper distance. In this case, the electromechanical system is a costly system, the sensors still require calibration, and the wear and tear still exists causing maintenance or replacement costs, along with loss of accuracy and precision.
Solving the Sensor Repositioning Issue
A Two Sensor Solution
One solution for this problem is to have two sensors that have a wide enough sensing range that allows handling different widths without having to reposition the sensors. You would still have to deal with sensor calibration, but the elimination of sensor repositioning might be enough. However, adding a system that does not require calibration certainly provides a great bonus to the application.
A Single Sensor Solution - is it possible?
A second solution would be a sensor wide enough that would cover the entire width of the web. Sensor repositioning is eliminated completely, even though sensor calibration is still required.
Our Solution - Wider Sensing Ranges and No Calibration
We have a solution to all these problems. Ever since we launched our technology in the Converting industry, our main differentiator has been our sensor technology. We are able to offer a sensor that has multiple applications, with a very manageable number of models based on sensing ranges and light sources. Any of our sensors can be used for width measurement and monitoring by the edge of the web or a constant contrast within a web, such as a printed line. Better yet, our sensors do not require calibration, so you can use them on any material.
The single sided sensor compact design provides the converter with a sensors that is not subject to space restraints. Unlike fork style sensors, webs with greater material thickness are not an issue.
An Example of a Specialty Web Width Application with our Technology
We prepared a web width measurement and monitoring application for a customer in North Carolina that required a contrast sensing application to measure and monitor the width of a web within a clear coating. You can read more about this application in our website.
WPS 900 - The Widest Sensing Range in the Industry Provides a Single Sensor Width Measurement Solution
We recently launched WPS 900 sensor. At a sensing range of 900 millimeters (35.4 inches) it provides the widest sensing range in the industry. This means you can use a single sensor for center guiding or width measurement or both, for any width of material up to 35 inches. More important, its design provides a resolution of .127 mm or .005 inches, and allows you to monitor up to 256 different edges.
If you are interested in a width measurement application, schedule a live online demonstration from the comfort and safety of your office. If you would like to know more of our web guiding and monitoring applications, contact us to get our monthly ENews and other information as it becomes available.
Future topics: Edge curling, how it affects width measurement and what you can do about it.
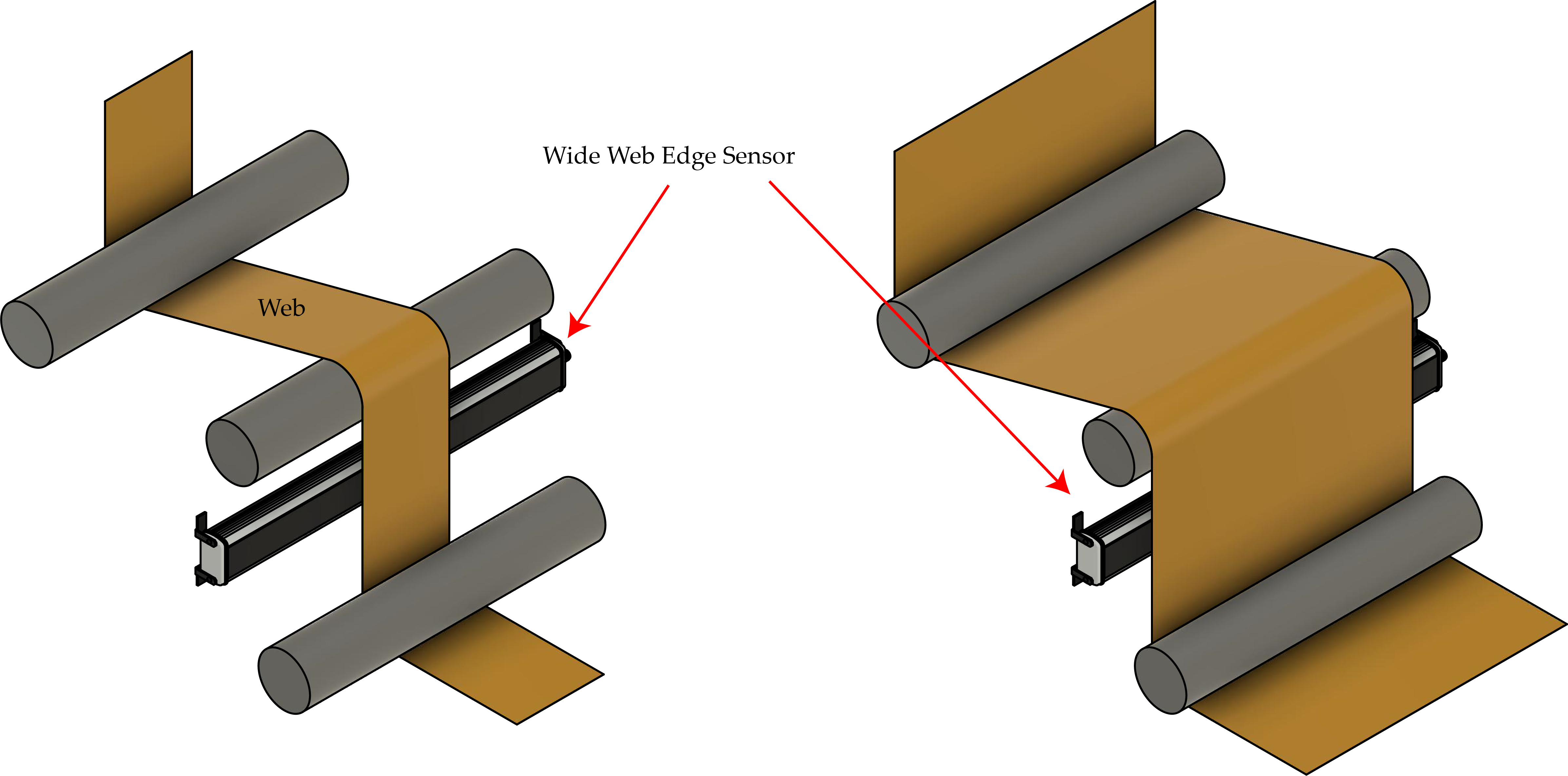