One of the most important components of a web guiding system are the sensors. If you can't measure, you can't control. If you have a poor sensor and are not able to measure the position of the web properly, it will be impossible to get the accuracy required.
Common Terminology in Sensors
The terminology used to address sensors in the converting industry is fairly extensive.
- Range, resolution, accuracy, linearity and deadband are terms used for performance qualities of sensors
- Sensor types can be classified by signal emission: infrared, optical, ultrasonic, air.
- Sensor types can also be identified by the feature of the web that is being detected: edge, line, contrast
- Update rate and frequency are terms used to describe how fast the sensor can measure
- Pass line and plane change are terms that are not used on most recent sensor technology, but older ultrasonic sensors will have issues with pass line changes. If the web is too close to the ultrasonic emitter the soundwaves might reflect the sound waves in a way that does not provide an accurate measurement.
- Temperature drift also affects ultrasonic sensors as the piezoelectric crystal used are sensitive to temperature changes.
The range of the sensor is the maximum lateral position change that a sensor can measure. Often in web guiding applications, range is not important mostly because of the fact that you are controlling. However, it is important when you are dealing with web width changes in the line. Range defines how much change in lateral position you can measure with the sensor.
Resolution is the minimum lateral position change that a sensor can detect. If you want to guide a web to 0.005" you will require a sensor with a resolution that is 2x to 4x higher than the guiding accuracy.
Accuracy is an indication of the closeness of the sensor measurement to the real measurement. This is important for certain types of sensors that are affected by different materials properties such as porosity and opacity.
Linearity is the consistency of the measurement over the entire range of the sensor
Why is sensing important?
Accurate guiding is impossible with inaccurate sensing
Material properties can affect sensing accuracy. As mentioned before, opacity, porosity and reflectivity are some of the web characteristics that will affect certain types of sensors. The environmental conditions can also affect sensing accuracy. Changes in temperature, airflow and the presence of a vacuum can affect a sensors accuracy or make completely inadequate for use. That is what the manufacturers of sensors based on the opposing beam technology have not been able to figure out.
Opposing beam technology
Most often you will encounter opposing beam sensors. These are commonly called "fork style", "u-shaped" or "horseshoe style." The basic operation of this technology is one arm has the emitter of the signal and the opposing arm has the receiver of the signal. As the web goes in between the two arms it blocks the signal up to the edge of the web. It is a simple principle and it works well in several applications.
The problem with these sensors is that depending the type of sensor there will be occasions in which the web will allow part of the signal to leak through when it is blocking the signal. This will affect the linearity and resolution of the sensor.
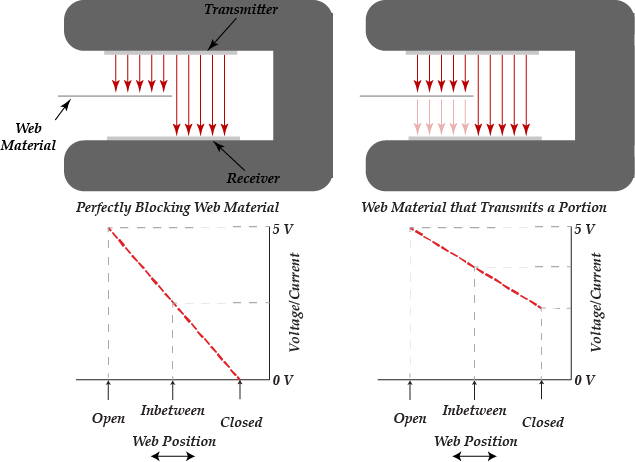
The signal could be air, sound, infrared light, visible light or uv light. This really doesn't matter. What matters is the material type, whether it is opaque, porous, or reflective. That is why manufacturers will recommend a different sensor based on the web material or the conditions in which the sensor will operate.
Disadvantages
As mentioned before, the main disadvantage of sensors based on opposing beam technology is that they are material dependent, and gain change occurs. This the reason calibration is required on sensors that use this technology.
Fiber optic sensor technology
This technology was introduced to the converting industry by our company in 2014. It has several advantages over the opposing beam technology in that it has higher accuracy and there is no gain change needed. It does provide an absolute measurement, the resolution does not depend on the range, and it is reliable with a variety of different materials. This eliminates the need for calibration due to changes in material properties and environmental conditions.
Roll-2-Roll Web Position Sensor Demo with Multiple Materials Video
We have much more information on fiber optic sensors, but we will discuss this information in future post. Meanwhile, contact us to find out more on fiber optic sensor technology. The following articles provide some in depth information on fiber optic sensor technology:
The Impacts of the Latest Developments in Sensing Technology
Our next blog post will address Controllers for web guiding in the converting industry
If you are interested in getting more information from our knowledge base you can contact us. If this article or any of the other blog posts were interesting to you like us on facebook, linkedin, twitter or youtube.
There is more information we can offer you to help improve your converting process!