Every generation has a revolution and for years U-shaped sensors were the standard in edge sensing technology. Now the next generation in web sensing technology is here. Materials are getting thinner, lighter and processes are getting faster. Is your web guiding technology up to date for this challenge?
Time consuming set-ups, inefficient processes to change materials, and lack of precise edge detection because of web material property changes are some of the major problems faced in the converting industry. One of the innovative technological developments of 2015 addresses these problems providing a major leap in web guiding through a new sensor technology.
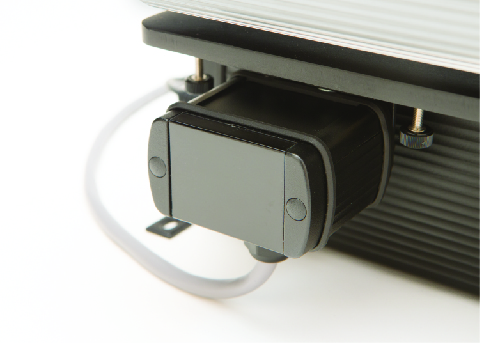
To the converter, faster speeds and thinner materials mean more production at less cost. At the same time, it presents an interesting challenge to web guide manufacturers as sensors have a more difficult task in detecting the edge. Web guiding is one of the important, yet often overlooked, material control components, and the detection of the position of the web is of great importance. As such a major element in the material handling, web guides need to react faster to the disturbances present in the converting process.
At the end, what this translates to in the converting industry is operational problems such as misprinted materials, misplaced layers of material, material wrinkling or tears, and manual adjustments of the sensor controls due to changes in material thickness, and product aesthetic problems such as misplaced resealable closures. All in all time, money and products are wasted with inaccurate sensing technology. The new technology eliminates these problems for the converting industry.
Today’s sensor technology is based on the principle of signal blocking. They provide a relative, inferred, analog measurement. Sensor systems based on this principle depend on the assumption that the material is 100% impermeable to the emitted signal. However, materials are often not 100% impermeable and this requires calibration of the sensor for each type of material. Furthermore, this type of technology can only infer the position of the material. When the material characteristics change the sensor will detect the signal but the position of the material is wrongly inferred. Every time the material characteristics change, the sensor has to be recalibrated to a new percentage of impermeability.
The blocking principle requires an emitter in one arm and a receiver in the opposite arm. The web runs between the arms and blocks an ultrasonic, pneumatic, or infrared signal.
Until now, sensors that operate under the blocking principle have saturated the market. After more than ten years of research and development, Roll-2-Roll Technologies LLC, has come out with a commercial web edge sensor that uses the light scattering and spatial filtering technology to accurately measure the web edge position.
The new sensor technology with the light scattering and patented fiber optic sensing principle provide a true, absolute, precise, and digital position measurement of the web. The fiber optics act as filter that allows only the light signal that is in direct line with the fibers. A one dimensional pixel array collects and converts the light into digital voltage signal which is processed using an advanced digital signal processing algorithm. Unlike the current sensor technology, the fiber optic sensors have the ability to detect the true edge of any type of material without the need for any manual adjustments of the sensor.
Extensive testing has proven the capability of the sensor to be used with any material without calibration both in static and closed loop setup. Results confirmed the ability of the sensor to accurately detect the material, and in combination with the control algorithm of the guide, correctly position the material under various simulated disturbances. Additionally, the true edge detection allows for higher precision and accuracy in web position correction. The new sensor technology allows for a true precision of 0.0635, which the current technology cannot provide. Additionally the sensor can be used for edge and center guiding, depending on the application required. Another key feature of this sensor technology is that the same sensing principle can be used for line sensing, contrast sensing, thread detection and counting. Unlike the traditional line sensors or contrast sensors, the new fiber optic sensor technology does not require any teaching and is unaffected by the ambient light conditions and reflective properties of the material.
In general, fiber optic sensors offer the converting industry an easier transition into higher speeds and thinner materials by providing a sensor that is more accurate and has the capability of handling different types of materials, or even materials that change characteristics within a roll during a production run. Moreover, this sensing technologies allow converters to reduce equipment inventory since one sensor can be used for multiple applications, such as line, contrast and edge guiding, where a combination of ultrasonic, infrared and pneumatic sensors might have been required. However, there are other benefits that this technology opens. Higher precision opens opportunities for material savings as tolerances become tighter in order to run materials with narrower widths.