Why is a web guiding system needed?
Web material transported within converting machines will not always track straight. A web guiding system is required for proper alignment of the material.
A variety of factors such as, poor quality raw materials, material property variations in raw materials, improper machine alignment, improperly maintained machines, environmental conditions, and processing conditions, cause lateral web misalignment as they are transported in the converting machines/lines. Lateral variations due to poor quality of raw material include telescoped rolls, poorly wound rolls with lateral misalignment (see image below), cambered webs, raw material with web thickness variations, etc. Even if the raw materials are perfect, process variations in speed and tension might cause changes in traction that steer the web improperly. Finally, roller misalignment, changes in roller drag and air entrainment between the web and roller can cause lateral misalignment.
Web materials are not perfect, and neither are converting machines.
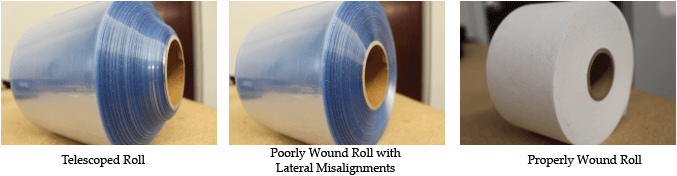
Aligning the flexible web material over the rollers (cross machine direction or the lateral direction which is along the width of the material) during transport within the manufacturing process is critical to most converting applications. Often, wastes such as wrinkling, creasing, misregistration (both print and material), and at times web breaks are attributed to web alignment issues during transport. Reducing these wastes improves the productivity of the manufacturing process.
What is a web guiding system and where is it needed?
Web guiding system is also referred to as web guides or lateral guides. These devices are used in aligning the flexible material roll-to-roll converting machines. As the name suggests, the device guides the material to the desired position. Web guides are used in different locations within the manufacturing machines based on the process requirement. Web guides in the intermediate processing areas are called intermediate web guides. Web guides used at the entry or exit of the manufacturing machines are terminal web guides.
Intermediate web guides are typically used before or after a process where material positioning is required; web guides at the end of a long oven or at the entry of a coating or printing process are common locations for intermediate web guiding. Unwind guides are used to position the material coming off a material roll at a correct location within the machine while a rewind guide is used to wind rolls with good roll edge quality. No matter where the web guide is used, the function of the device is to ensure proper alignment of the material within the machine or on a material roll.
How does a web guiding system work?
As the flexible material is transported over rollers, the web tends to align itself perpendicular to the axis of rotation of the rollers (see the animation on the right). This is called the normal entry rule and this is the reasons for web misalignment when the rollers in a converting machine are not aligned properly.

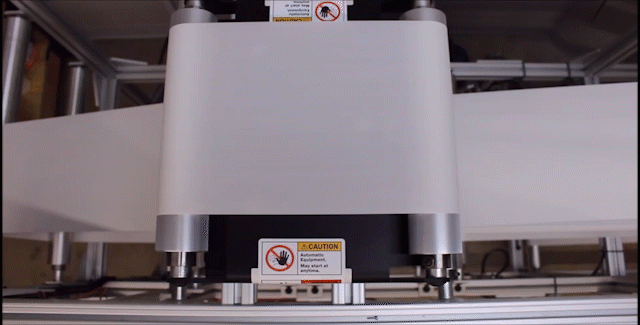
Web guides that align the material use the same normal entry principle (see Figure 3). By deliberately changing the axis of rotation of the guide roller, the web guides steer to a different position. Several types of web guides are used to align the web; the difference is in the way the axis of rotation of the roller is changed.
What are the components of a web guiding system?
Web guides are often electro-mechanical (and for some applications there are electro-pneumatic, or electro-hydraulic or completely pneumatic) devices that automatically control the edge or the centline position of the web within the machine. There are three main components (see Figure 4) of a web guide: (1) sensor(s), (2) controller, and (3) guide mechanism. The sensor is the vision to the system used to sense the actual/current position of the web material. Different types of sensors are used to measure the lateral position of the web material. The type of sensor is usually based on the type of web material and the processing application. The position information from the sensor is then sent to a controller which is the brain to the guiding system. The controller processes the sensor information and determines the required corrective action for the guide mechanism in order to guide the material to the required position. The controller then commands the actuator, which is part of the guide mechanism, to physically steer the web material to the desired location. Typically the controller is an electronic hardware; electrical and pneumatic controllers are seldom seen in practice today.
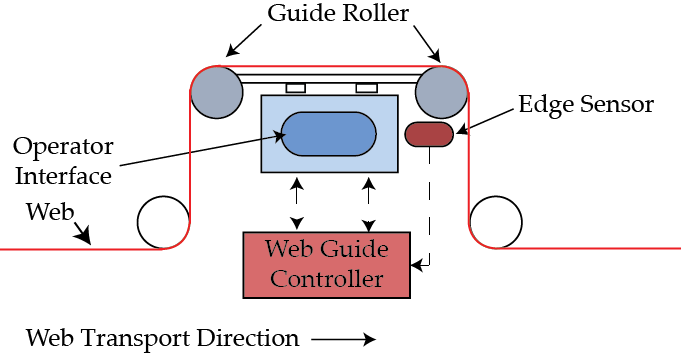
The web guiding system is essentially an automatic control device that constantly corrects the position of the web based on the sensor measurement. The effectiveness of this control system is dependent on all the three main components of the guiding system. If any one of the component is faulty the overall guiding system will be ineffective.
Choosing the Best Web Guiding System for your Operation
As we search for the most appropriate equipment for our operation, we are faced with the task of selecting from myriad options based on technical data and specs. Through these data, measurements of accuracy, precision, linearity and resolution, manufacturers are trying to present the benefits of their products based on the device’s performance profile. However, sometimes what appears to be the best offer, based on what looks to be the best technical data, might not really be the best. The technical data can even be irrelevant information when considering performance. See performance indicators relevant to your system and how to apply this information to your applications.