A customer once asked us why would you need web guiding on a brand new machine? Their point of view was that the machine was state of the art, the web guide didn't move at all during operation, and they didn't see any problems with their materials. Well, our answer was that there are four main reasons why any converting line requires web guides.
- Materials are not perfect
- Machines are not perfect
- Processes are not perfect
- Operators are not perfect
Materials are not perfect
When dealing with materials in converting, the first thing we need to consider is that the material already comes from a previous process. A typical issue that converters face are poorly wound rolls. This could be the result of tension control issues from the supplier of the roll. However, this condition might be detected or not.
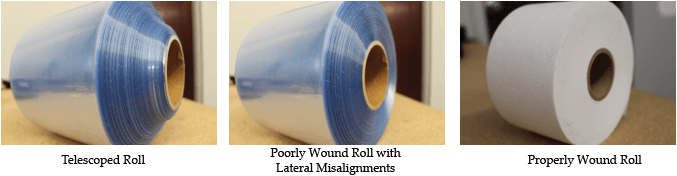
Then, you might have to process a roll that has been deliberately oscillated during the roll process. This is usually seen in operations where the material has a border that differs in thickness from the rest of the web, such as in lamination or coating processes. Material thickness variations might be present from the natural manufacturing process of the roll. These gage band variations can occur across the width of the web. These thickness variations can cause the web to track or slide differently, causing slight changes in position of the edge of the material. A poor splice that causes step or angular misalignment might be present at the joining of the end and start of rolls which can cause a sudden misplacement of the edge of the web. Additionally, some materials might have a natural curvature, which is also known as camber.
Machines are not perfect
One of the most common reasons for webs not travelling properly has to do with the rollers on the machine. Out of round rollers will affect the behavior of the web. Out of round could be rollers with excessive eccentricity, variations in roller diameter across the length of the roller or roller profiles with excessive camber. Additionally, rollers might be misaligned with the other rollers in the machine causing the web to track side to side
Converting machines can also have issues of poor tension control. When the web does not have enough tension, it will have issues of tracking through the machine. Acceleration or deceleration of the web will also affect how the web tracks through the machine.
Processes are not perfect
A web that presents gauge variations, which could be caused by coating or lamination issues, will have issues with miss-tracking. Another factor, specially with higher web speed conditions is air entrainment between the roller and the surface of the web. The air in between these two components will create a film that will reduce the friction and therefore allow for slippage of the web on the rollers.
Operators are not perfect
Splicing requires a precise alignment of two webs and holding them together with a splicing tape. However, precision does not occur often and it will be necessary to provide a web guiding system. Also, operators might not position a new roll at a precise location on an unwind stand. This will create a need to constantly guide the material to maintain it in position with the machine.
Because of all this conditions, web guides are necessary at different locations of a roll-2-roll machine just before the process that requires web alignment.
Every year we present webinars related to web guiding and web monitoring. To get more information as to when these will be held and attend, just contact us and tell us that you would like to get more information on signing up for our webinars. Read more in our article: Web guiding system: Why, What, Where and How?
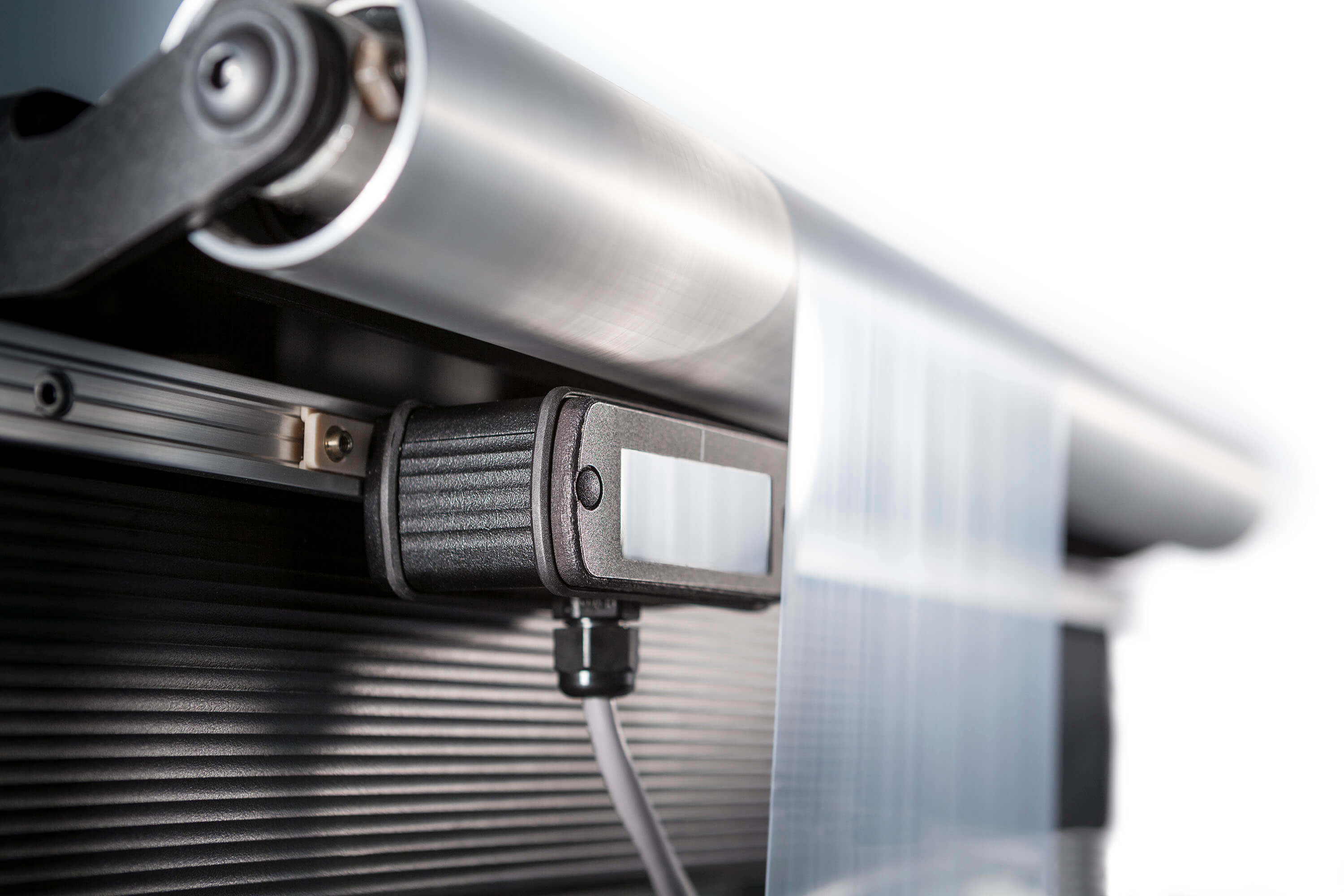