Introduction
In a previous whitepaper the disturbance rejection performance of Roll-2-Roll Technologies' web guides was reported for sinusoidal and step disturbances. This whitepaper reports the performance of the same web guide with a high speed actuator along with an improved sensing algorithm. A new high performance actuator with a maximum linear speed of 172.35 mm/sec and maximum displacement of 45 mm is used with a high performance chopper drive with 256 microstep resolution. Modifications to the web guide mechanism to reduce transmission compliance was also made to improve the performance. The improved high performance web guiding system is intended to be used in demanding high speed, low tension converting applications such as diaper and adult incontinence manufacturing. The detailed specification of the web guide is shown in Table 1 below.
Specification | Dimension/Value | Units |
---|---|---|
Roller Width | 254 | mm |
Maximum Correction | 45.25 | mm |
Displacement Resolution | 0.000248 | mm |
Maximum Linear Speed | 172.35 | mm/sec |
Maximum Linear Force | 133 | N |
Sensor Resolution | 0.0635 | mm |
Sensing Window | 16 | mm |
Sensing Frequency | 100 | Hz |
Control Frequency | 100 | Hz |
Sensing Algorithm Improvements
The previous sensing algorithm used was a simple Gaussian digital signal processing algorithm to detect the web position. Even though the algorithm was robust it was affected by optical design issues that reduced the sensor resolution to be about 0.3175 mm instead of 0.0635 mm. An advanced digital signal processing algorithm that automatically adjusts to the web material has since been implemented to improve the sensor resolution. Essentially the new algorithm self calibrates or adapts every sampling time to provide the most accurate measurement. The results from experiments quantify the sensor resolution to be 0.0635 mm and linearity error to be less than ± 1% is reported in the white paper titled “Material Agnostic Fiber Optic Web Edge Sensor.”
Controller Optimizations
Several controller optimization algorithms were tested and implemented in the new web guiding system. Optimizations to acceleration profile, velocity profile and position profile for the web guide were carried out to obtain the best performance for the web guiding system. Controller can now use either position or velocity based control system, with in-built current control in the high performance stepper motor driver.
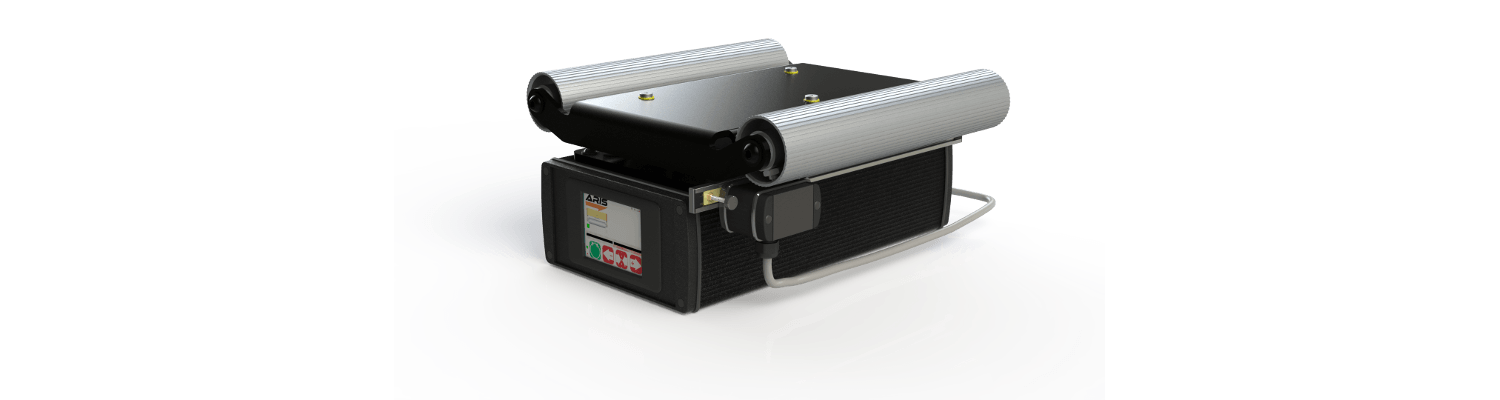
Web Guide's Mechanical Design Improvements
Mechanical design improvements to reduce the compliance in the transmission, reduce inertia of the guide mechanism, reduce friction in the guide rails and to install the sensor as close to the guide roller as possible were made.
Experimental Roll-to-Roll Machine
In order to quantify the guiding performance we test the web guides in an in-house closed-loop roll to roll experimental platform (see Fig. 2). The length of web material threaded in the machine is about 20 meters and the web can be transported at a speed of up to 10 meters/sec. The web tension in the machine is maintained using a pneumatic dancer system. Webs with 100 mm and up to 450 mm in width can be transported in the machine which is equipped with two web guides. Two spans with a total length of 1200 mm separate the two web guides. For experimental purposes the upstream guide is used to create disturbances while the downstream guide is used to correct for the disturbances.
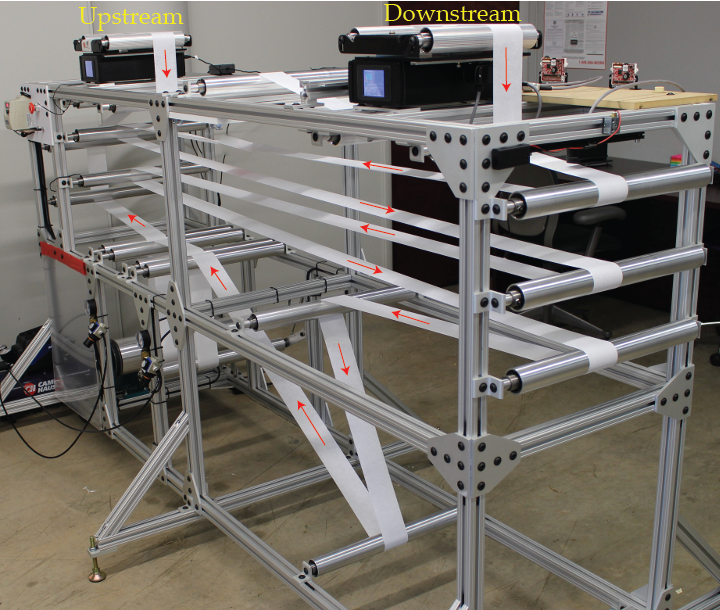
Two additional sensors, with a sensing window of 16 mm (see Fig. 3), are used to measure the lateral position before and after the downstream web guide. These sensors provide a clear quantification of the magnitude of lateral disturbance entering the web guide and the corrective response of the web guide.
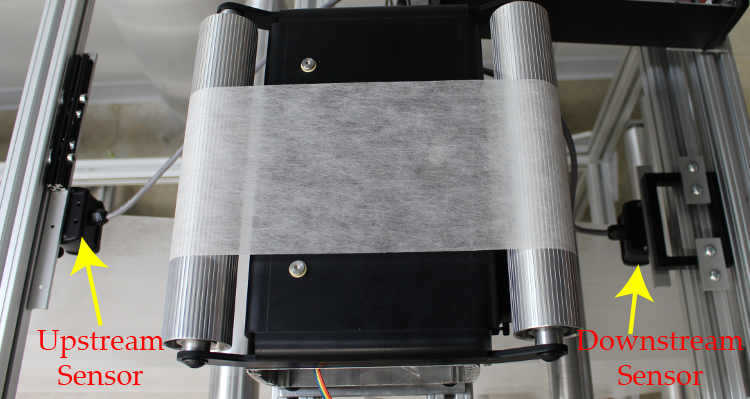
Sinusoidal Disturbance Rejection
Sinusoidal disturbances are common lateral errors seen in industrial converting machines. Hence the performance of the web guiding system is evaluated for sinusoidal disturbances. In the experiments reported in this white paper, sinusoidal lateral disturbances with a magnitude of 8 mm and frequencies of 0.25 Hz, 0.5 Hz, 1 Hz, 2 Hz and 4 Hz were introduced with the upstream guide while the downstream guide is used to correct for the disturbances. A nonwoven web of width 130 mm was transported at a speed of 6.6 meters/sec (1300 feet-per-minute). The web tension in the machine was maintained using a pneumatic dancer system.
A summary of the time domain results are shown in Fig. 4. The plots show the disturbance entering the guide roller (measured using the upstream sensor) and the performance of the web guiding system (measured at the downstream span using a sensor). A FFT of the lateral disturbance and the guiding performance is shown in Fig. 5 with the Table 2 that further summarizes the results.
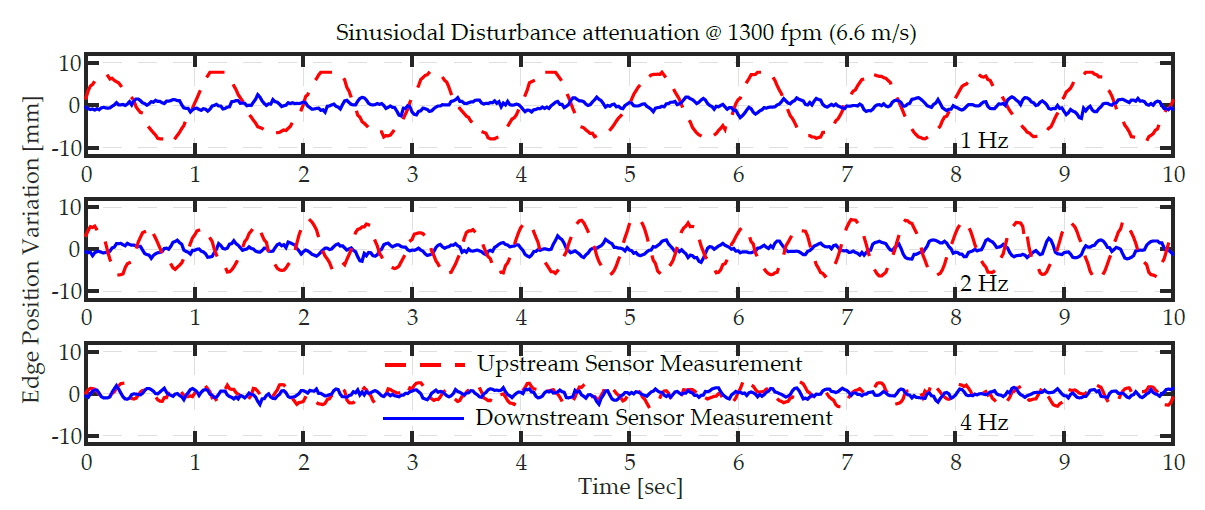
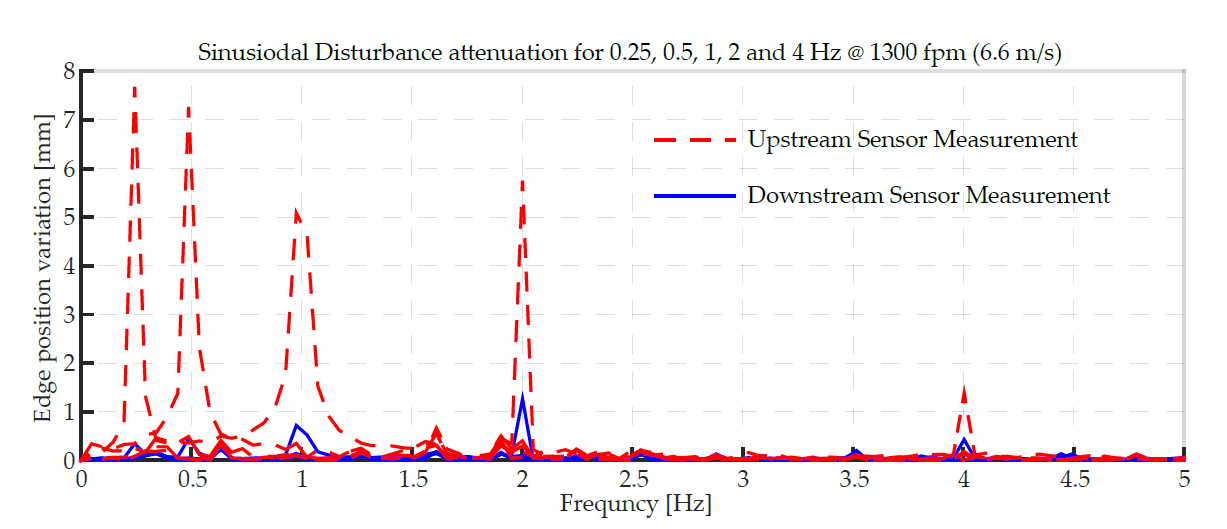
Disturbance Frequency (Hz) | Upstream Sensor Measurement (mm) | Downstream Sensor Measurement (mm) | Attenuation % |
---|---|---|---|
0.25 | 7.68 | 0.34 | 95.57 |
0.5 | 7.27 | 0.49 | 93.26 |
1 | 5.09 | 0.72 | 85.85 |
2 | 5.75 | 1.27 | 77.91 |
4 | 1.39 | 0.43 | 69.06 |
Summary and Conclusions
Significant improvement in performance was achieved with the improvements due to the new actuator, modifications to the sensor algorithm, optimization of the controller parameters, and improvements to the guide mechanism. Especially at frequencies between 1 to 4 Hz a significant improvement was observed. The previous control system was unable to attenuate the disturbances at these frequencies. However it is noted that these performance improvements will be added to the standard ARIS Web Guiding System only when such performance is absolutely needed.
In order to reject the high frequency disturbance the acceleration and velocity profiles of the controller were optimized to be at their maximum limits. High acceleration profiles require low inertia of the guiding system which implies the tension on the web guide should also be low. Hence care must to taken to ensure that the guide mechanism is not overly loaded when these high performance controller parameters are used.
The most significant loading of the motor occurs during direction change. The motor has to overcome the inertia of the guide mechanism to the stop the guide and to start accelerating in the other direction. And as the frequency of the disturbance increases the loading duty cycle also increase. A high duty cycle loading with a DC or a Brushless DC motor may result in actuator failure. The DC motors draw current based on the load on the motor. As the load increases or the duty cycle of the load increase, higher current is draw which may result in overheating and actuator damage. Stepper motors on the other hand draw a constant current and will stall if the load is excessive. This prevents the motor from overheating and prevents actuator failure with high frequency disturbance.
The high performance stepper motor driver in ARIS Web Guiding System is optimized to prevent stalls and for load-adaptive current scaling to reduce the energy consumption. This prevents the overheating issue while providing maximum efficiency. Higher acceleration profiles can be achieved by increasing the coil windings, using a bulkier motor with a high throughput current driver. All of these will increase the overall size of the actuator and the power consumption of the ARIS Web Guiding System.
An alternative to using a high performance actuator is the use of a standard web guide with a properly designed web path. The inherent filtering (or absorbing) nature of the web can be exploited to reduce the disturbance propagation. The simplest option would be to have long web spans which can absorb high frequency lateral disturbances. Such a design would be a reliable cost effective solution compared to using a bulkier high speed actuator which may be prone to actuator failure.