What are Pneumo-Hydraulic Web Guides?
Many displacement guides, steering guides, unwind / rewind guides manufactured in the 1960’s, 1970's, 1980’s and 1990's were controlled using both pneumatic and hydraulic control systems which are often referred to as pneumo-hydraulic web guides. These web guide were really common before the mass adoption of the electronic (analog and digital) controllers and electric actuators. A lot of these units were predominant in blown film lines, extrusion lines, flexographic printing presses and even in paper converting machines.
Pneumatic Sensors
The pneumo in the pneumo-hydraulic web guides refers to the air signal used by the web edge sensor. The sensor typically has two pneumatic lines: a pressure line, that provide pressurized air to the sensor, and the signal line, that collect the attenuated signal from the sensor to the control unit. The web edge position is determined by observing the change in air pressure while a web material is passed in between the throat (fork or the arms) of the sensor. The control unit typically has an air pressure adjustment system which maintains the required pressure for the sensor to work effectively. In order to maintain proper pressure it is recommended that the pneumatic lines are as close to the control unit as possible and typically no more than 12 feet or 3.65 m.
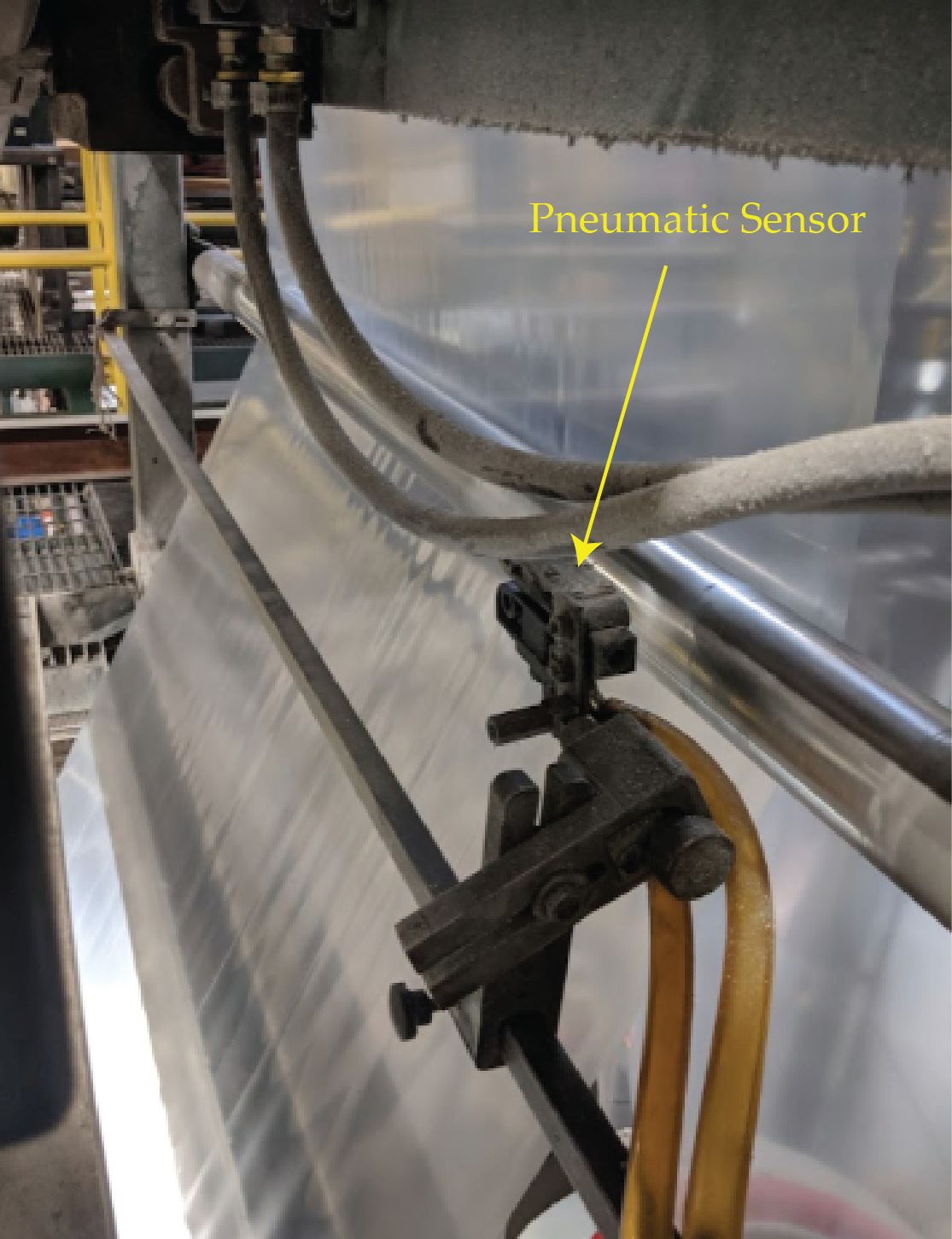
Working Principle of a Pneumatic Web Edge Sensor
These web edge sensors work on a very basic sensing principle: the amount of signal received by the signal line is directly proportional to the location of the web inside the sensing window. When the web is completely outside the sensing window, pretty much no signal is attenuated. As the web edge moves inside the sensor window, the air signal is blocked and hence the signal attenuates. The magnitude of signal attenuation provides a signal proportional to the location of the web edge.
Advantages of Pneumatic Web Edge Sensors
These web edge sensors have several advantages, mainly because of the type of signal used for web edge detection. Unlike optical sensors, these sensors are not affected by the opacity of the materials. Moreover, since a constant stream of air is flowing through the sensor throat, these edge sensors are not affected by the dust in the environment. Finally, with air being the only signal, these sensors can be used in hazardous environments since they are intrinsically safe. The advantages of these web edge sensors are summarized below:
-
Clear and opaque homogeneous materials can be detected by the sensor
-
Unaffected by dust
-
Intrinsically safe and may be used in hazardous environments
Disadvantages of Pneumatic Web Edge Sensors
In spite of some advantages, these pneumatic edge sensors are not a popular sensor of choice for new builds. There are several reasons to avoid these sensors.
One of the main reasons to avoid pneumatic edge sensors is the accuracy of the measurement. Accuracy is an indication of the closeness of the sensor measurement to the true/real position. Since the sensor responds to change in air pressure (due to web movement) the accuracy of the measurement depends on the ability to maintain a steady air pressure. Often this is an issue with clog, line pressure drops, etc. The second main reason to avoid this sensor is its limited resolution. The resolution is the minimum difference in web position that can be perceived by the sensor due to the pressure change. This resolution is highly dependent on the quality of the air pressure line and even the web material being detected. The third reason to avoid these sensors is the limited sensor range. Range is the maximum web position variation that can be perceived by the sensor. Typically these sensors have a range of no more than 0.5 in or 12.7 mm, since wider range would affect the minimum pressure required for the sensing principle to work.
Apart from these key disadvantages, the pneumatic web edge sensors also have some other shortcomings or annoyance. These sensors are often bulky, rigid and heavy. So moving them around is not an easy task. Even if they can be moved, they have to be located close to the power unit because of the pressure line requirements. Typically they are recommended to be no more than 12 ft of the supply line. Since these power units are noisy, the environment around these web guides are noisy as well. Sometimes the sensor may be clogged because of contamination and this can significantly affect the web guiding performance. Finally the sensor throat, the distance between the two arms or forks, are typically small in order to maintain the required pressure. Small throats are often an issue while threading the web after a changeover. Moreover, small throat can also snag a splice with a tail, potentially causing damage to the web or the sensor itself.
Finally, the sensors are not suited for certain environments (vacuum) or with certain materials such as porous materials, or delicate materials. To summarize the many disadvantages with the pneumatic web edge sensors are:
-
Inaccurate sensor measurement
-
Low resolution
-
Small range
-
Bulky, rigid, heavy and not easy to move around
-
More maintenance required than electronic sensors
-
Not suited for vacuum environment
-
Not ideal for porous materials or delicate materials
Hydraulic Actuators
The hydraulic in the pneumo-hydraulic web guides refers to the hydraulic actuator which includes a hydraulic cylinder powered by a hydraulic power unit.
Typically a hydraulic power unit and the control system includes a reservoir for the oil, a hydraulic pump (powered by an AC motor) with filters and pressure gauge, a servo valve that controls the flow of oil to the hydraulic cylinder, and the hydraulic lines that supply the oil to the hydraulic cylinders. Depending on the power requirement, the complete hydraulic power unit may weigh from 100 lb (45 kg) to about 250 lb (113 kg).
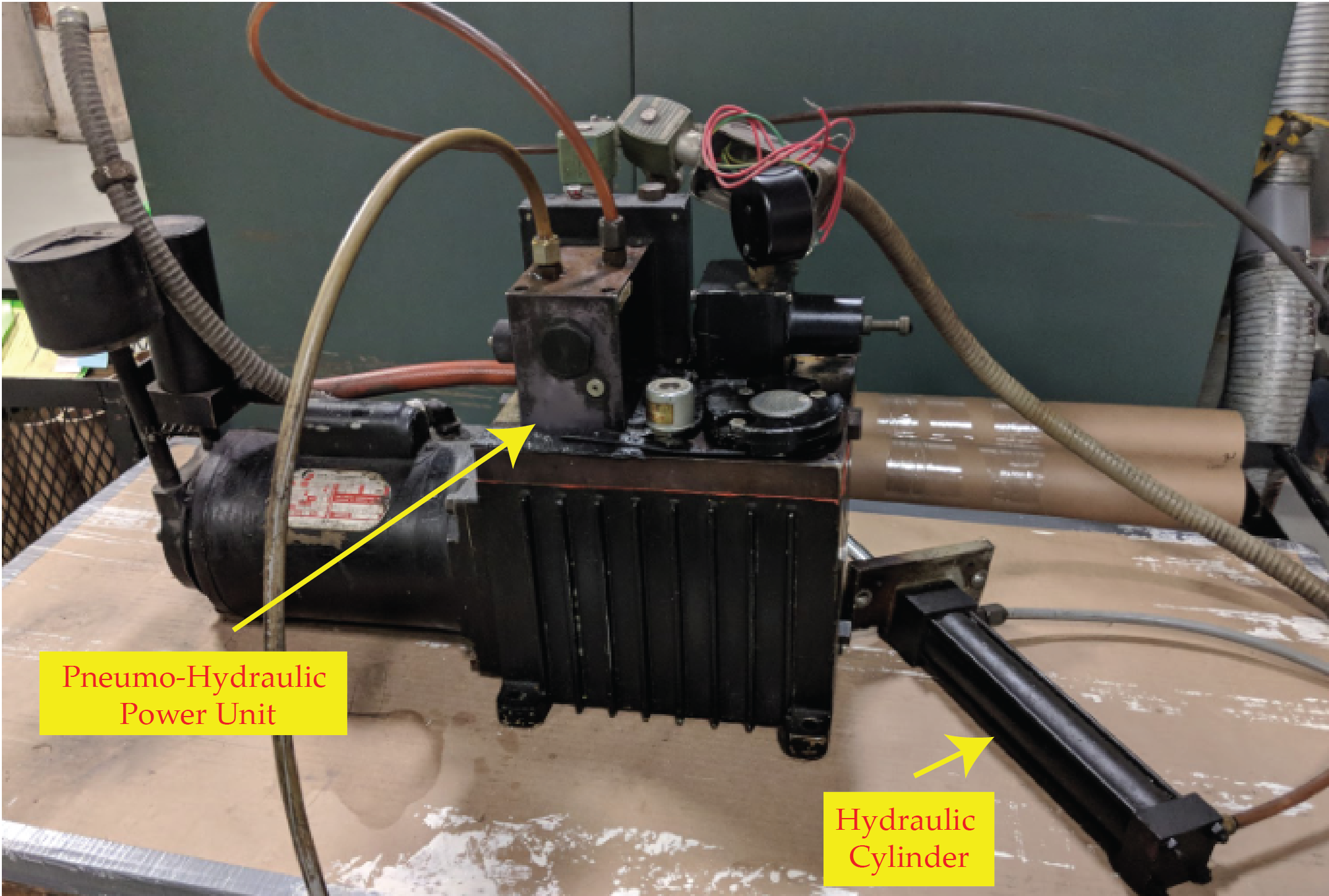
The servo value is the controller in the pneumo-hydraulic web guides. The signal from the pneumatic sensor is used by the servo value to direct the hydraulic fluid through the two hydraulic lines to position the hydraulic cylinder (or the web guide) at the desired location.
Advantages of Hydraulic Actuators
The main advantage of using hydraulic actuator is the larger amount of thrust or force the actuators can deliver. Higher thrust in turn means that the actuator can reach higher acceleration or high correction rates quickly. The web guide response can be high with hydraulic actuators. Hence these actuators are still predominantly used in metal lines where the mass or the load the web guide needs to move is large.
Disadvantages of Hydraulic Actuators
Nowadays the use of hydraulic power units are becoming less common because of a variety of disadvantages.
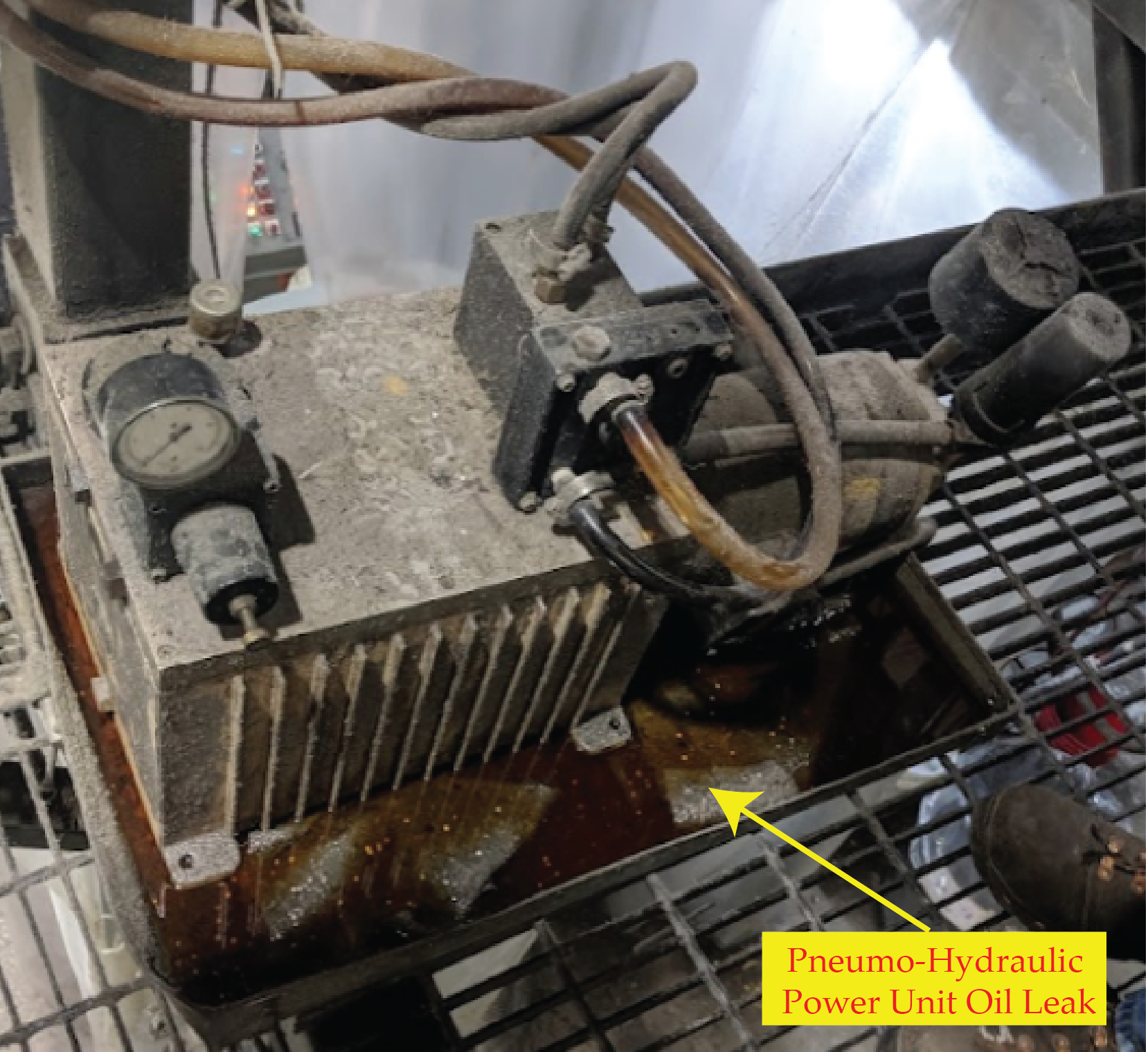
Leaks are the biggest problem with pneumo-hydraulic web guides. The leak in the high pressure system is not about “if” but “when” a leak would occur. Hydraulic oil leak can happen at the power unit or at the cylinder and anywhere in between. And the leak can occur due to seal failure, gasket failure or o-ring failure or pressure line failure. The leaks cause a mess, safety hazard with slippery surface. More importantly they contaminate the previous product that is being manufactured in the production line. All of these directly affect the bottom line of the operation.
Apart from the leak, these systems are also costly to operate, needing frequent maintenance. It is necessary to change the seals, gaskets, o-rings, filters, maintaining clean oil, flushing the system, etc.on a periodic schedule. The maintenance budget includes the cost associated with spare parts, consumables as well as the downtime required for preventive maintenance.
Even though the hydraulic units can provide high thrust at incredible acceleration, they lack precision and repeatability. With problems maintaining constant pressure in the system, the repeatability and precision are the scapegoats. It is also not uncommon to see the actuator move at different speeds based on the direction of the stroke. This is mainly due to the imbalance in the servo control value. This does affect the overall guiding performance.
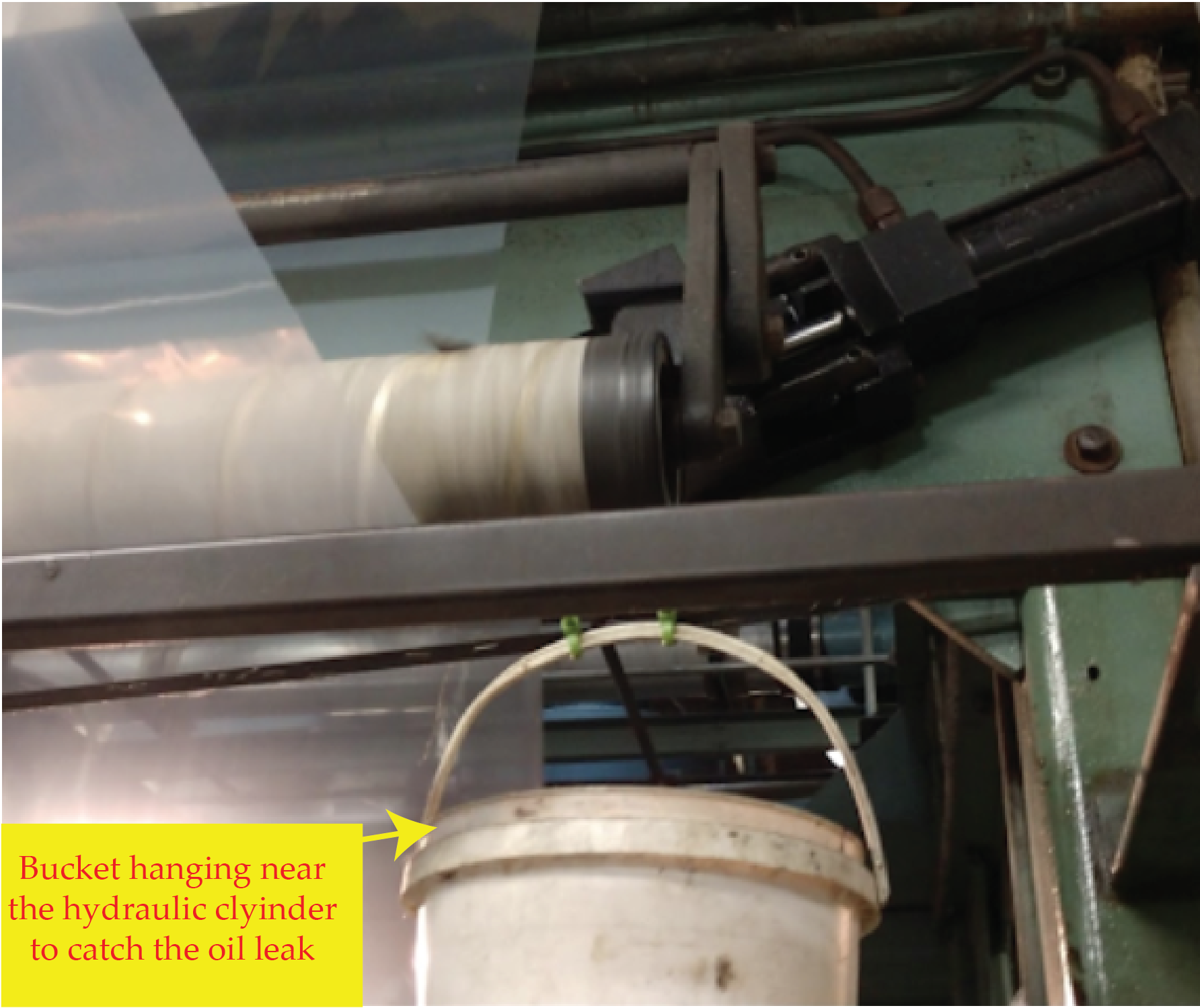
Similar to the pneumatic system, the hydraulic system is also affected by contamination, i.e., contamination of oil, clogging, etc. Overall the disadvantage of the hydraulic actuators or hydraulic control systems are:
-
High maintenance cost
-
Leaks causing mess, slip hazard
-
Contamination of the product and the environment
-
Repeatability issues and precision issues
-
Overall high cost of ownership
The hydraulic web guides are overly complex for most applications where the thrust requirement is below 2000 lbf (9000 N). The disadvantages outweigh the benefits and for applications with less than 2000 lbf thrust, electric actuators with electronic control systems are the best choice. The state-of-art sensors, controllers and actuators can provide a significant performance improvement at a fractional of the overall cost of ownership of the pneumo-hydraulic systems.
How to Stop the Bleeding?
If you operation is still relying on pneumo-hydraulic units you might be leaving a lot of money on the table. Consider upgrading to the latest in the sensor, controller and actuator technology with retrofit kits from Roll-2-Roll Technologies. The retrofit kits are designed to keep the existing guide frame structure while replacing just the sensor, actuator and the controller. This upgrade would be less than what you would need to rebuild the pneumo-hydraulic system. Best of all your don’t have to rely on the old technology to keep your line running.
Call us today to find out more about how we can help with this upgrade.